Page 1 of 2
Re: White Metal Soldering
Posted: Fri Jul 20, 2018 2:33 pm
by tom_tom_go
I see, thanks Jimbo.
Re: White Metal Soldering
Posted: Fri Jul 20, 2018 7:40 pm
by Big Jim
A few more images from today's activities on the metal melting front.
Just to prove that things don't need to get too hot while using lowmelt.
A close up without the iron in the way, my fingers are in the position I held the bits in while applying the iron.
By tacking the pieces on the inside you can make sure they are in the correct postition before you run a fillet down the joint and if you solder on the inside, no cleaning up required.
The last pic is my handy solder stick holding tool. Invaluable when you run out of hands.

Re: White Metal Soldering
Posted: Fri Jul 20, 2018 8:03 pm
by tom_tom_go
More stupid questions, you mention tacking but what are you using in that pic to do that?
Re: White Metal Soldering
Posted: Fri Jul 20, 2018 8:11 pm
by Big Jim
Not a stupid question at all.
Tacking is just using a small amount of solder on the tip of the iron to get the joint to hold. No real strength in it but enough to keep it all together.
(Iffy diagram coming up)
If you were joining parts A & B you might tack at the points marked X.
You can then check it is all in place, adjust if needed and then run a fillet of solder down the whole join.
If it is not correct and it does need taking apart again it is easier to split parts and clean it before you fill the whole lot up with solder.
Re: White Metal Soldering
Posted: Fri Jul 20, 2018 9:04 pm
by tom_tom_go
Ah, I call that tinning rightly or wrongly.
I thought tacking was holding a piece in position somehow which I have always found difficult when it comes to soldering brass together.
Re: White Metal Soldering
Posted: Sat Jul 21, 2018 6:54 am
by philipy
tom_tom_go wrote: ↑Fri Jul 20, 2018 9:04 pm
Ah, I call that tinning rightly or wrongly.
Tinning is what you might call "pre-soldering", applying a thin layer of solder to the individual pieces to be joined so that when you put them together and apply the iron again, the solder flows together easily giving a neat complete seam. This means, particularly if the pieces are big, you are only trying to heat half the total metal involved and its quicker and easier.
Tacking, as Jim said, is just a few blobs of solder to hold things temporarily. So yes, you're right, it is holding things temporarily, but using solder, not other things
In my piece about signal ladder construction, I said I tinned the rail length on one side, folded it in half and then tacked at 2 or three places to hold it. Subsequently using the iron again to split the tacks. The tinned sides then made it much easier to solder the rungs to the sides.
Re: White Metal Soldering
Posted: Sat Jul 21, 2018 9:04 am
by tom_tom_go
Thanks Phil.
Once upon a time you learned all this in school...
Re: White Metal Soldering
Posted: Sat Jul 21, 2018 10:02 am
by philipy
tom_tom_go wrote: ↑Sat Jul 21, 2018 9:04 am
Thanks Phil.
Once upon a time you learned all this in school...
Yup, I did! ( Well most of it anyway)
Re: White Metal Soldering
Posted: Sat Jul 21, 2018 11:57 am
by ge_rik
philipy wrote: ↑Sat Jul 21, 2018 10:02 am
tom_tom_go wrote: ↑Sat Jul 21, 2018 9:04 am
Thanks Phil.
Once upon a time you learned all this in school...
Yup, I did! ( Well most of it anyway)
I was only allowed to do woodwork ...... I really envied the metal bashers. Still, my mum and dad got a coffee table out of it (and a teapot stand).
Rik
Re: White Metal Soldering
Posted: Sat Jul 21, 2018 4:38 pm
by philipy
I was extremely fortunate that just as I entered the 6th form, my very enlightened school started a Technology Centre ( previously unheard of ) and took on a very talented and extremely clever chap to run it. I spent every moment that I could there ( probably accounting for my dismal A Level results but that's another story) . You could do/build practically anything you could think of but before you were allowed to do whatever it was, you had to complete the appropriate training courses depending on the project, i.e basic lathe work, basic aerodynamics, basic electronics, etc, then intermediate lathe work, advanced lathe work, etc .
The basic soldering techniques were hammered home by knocking 2" nails into a piece of wood and then soldering a 2nd one at right angles to each one. Until you could get a decent joint every time, you went no further!
Re: White Metal Soldering
Posted: Sat Jul 21, 2018 7:07 pm
by Peter Butler
How on earth I managed to be competent with any kind of handtools I will never know as it was all by trial and a fair amount of error. My first senior school had a choice of woodwork or metalwork and I chose the former. It taught me nothing! Advancement to grammar school continued my woodworking experience by making us sit quietly writing pages of notes on tree growth and other useless information but as for practical work.... very little.
My first entry into electrical installation to connect heating and lighting to fish tanks resulted in the fuse board being blown off the wall!
We all learn by mistakes and the lucky ones survive.
Soldering was a late starter and only came about during my modelmaking early years, long after schooling, which I never completed, having walked out before final exams and never returning. It is like all things.... practise makes (almost) perfect.
I have always encouraged my two sons to be practical and when my elder son was asked what he wanted for his 12th birthday he replied, an arc welder.... he got what he wanted and is now a very competent welder.
Re: White Metal Soldering
Posted: Sat Jul 21, 2018 8:17 pm
by GTB
ge_rik wrote: ↑Sat Jul 21, 2018 11:57 am
I was only allowed to do woodwork ......
Et moi aussi! I attended what was then called a high school and was in the professional group, ie. destined for Uni. We were taught French, in lieu of something that was actually useful......... Of course by the time my brothers attended the same school it was called a secondary college and 'trade' subjects like metalwork were on the curriculum.
Back on subject more or less, for other readers who were educationally deprived.
The tacking process Jim demonstrated is also the way to solder long seams in brass. Tack it in short sections until everything is straight and square, then go back and forth running longer sections of solder, until eventually the whole joint is complete. Otherwise, the metal expands and moves all over the shop if you try to solder it in one go.
Apologies to Jim if he intended covering the next bit and I've jumped the gun.
Whitemetal can also be easily soldered to brass (and other metals) with low melt solder. Low melt has poor adhesion directly to brass, but if you tin the brass first, the low melt bonds nicely to the ordinary solder and gives a strong joint.
Regards,
Graeme
Re: White Metal Soldering
Posted: Sat Jul 21, 2018 9:29 pm
by Big Jim
Graeme, you have saved me a job.
Any contributions are most welcome, hints, tips the lot. As I said in the first post, it is not how to do it, but how I do it and I may not be right.....
Re: White Metal Soldering
Posted: Sun Jul 22, 2018 8:44 am
by ge_rik
GTB wrote: ↑Sat Jul 21, 2018 8:17 pm
The tacking process Jim demonstrated is also the way to solder long seams in brass. Tack it in short sections until everything is straight and square, then go back and forth running longer sections of solder, until eventually the whole joint is complete. Otherwise, the metal expands and moves all over the shop if you try to solder it in one go.
Apologies to Jim if he intended covering the next bit and I've jumped the gun.
Whitemetal can also be easily soldered to brass (and other metals) with low melt solder. Low melt has poor adhesion directly to brass, but if you tin the brass first, the low melt bonds nicely to the ordinary solder and gives a strong joint.
Regards,
Graeme
Thanks Graeme and Jim. I wish I'd had this advice when I put together my IP Engineering Simplex. Would have saved a fair bit of trial and error.
Rik
Re: White Metal Soldering
Posted: Sat May 04, 2019 1:07 pm
by tom_tom_go
I finally got my temp soldering iron out to play and what a world of difference it makes, I will never go back to a standard iron!

- IMG_20190504_124854-01.jpeg (332.61 KiB) Viewed 16895 times
Cheap one off Amazon, comes with different soldering tips and a stand.
Allowed me to make a neat job of soldering capacitors to my Brandbright Circket motor:
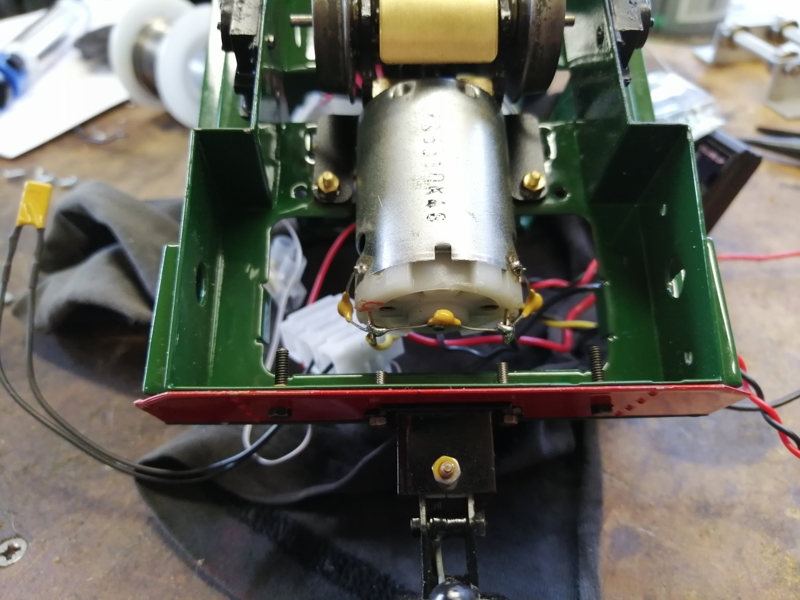
- IMG_20190504_124917-01.jpeg (291.68 KiB) Viewed 16895 times
Thanks for the suggestions!
What do you lot use to clean the tips after use? Years ago, I made the mistake of using files which you shouldn't do as that removes the protective coating off the soldering tips so this time around I don't want to ruin my new ones!
Re: White Metal Soldering
Posted: Sat May 04, 2019 1:37 pm
by GTB
tom_tom_go wrote: ↑Sat May 04, 2019 1:07 pm
What do you lot use to clean the tips after use? Years ago, I made the mistake of using files which you shouldn't do as that removes the protective coating off the soldering tips so this time around I don't want to ruin my new ones!
I'm not sure I could still solder with the old style hot electric poker. my father was taught to use what was basically a large lump of copper with a handle that he put in the kitchen wood stove to make it hot. He had one big soldering iron and one very big soldering iron. never have worked out why a lump of copper is called a soldering 'iron'. I watched him plenty of times, but it was well beyond my skills......
The old way of cleaning a soldering iron tip was to wipe it on a damp sponge, which is that yellow thing in the soldering iron stand. Some years ago I changed to using what is basically a brass scouring pad. It keeps the tip clean as a whistle, scrapes off excess solder and doesn't affect the tip temperature, or the tip coating.
Mine is made in Japan and came from a local supplier. It looks like this, but I would think the equivalent is available in the UK from electronics suppliers.
https://www.jaycar.com.au/goot-solderin ... r/p/TS1510
Don't be tempted to use a cheap stainless steel scourer from the supermarket, it is hard enough to damage the iron coating on the copper soldering tip. The iron coating is there to stop the copper tip dissolving into the solder.
If you will be soldering whitemetal as well as electrical work, get a separate tip for the lowmelt solder. If the two solders mix, you can get brittle soldered joints.
Regards,
Graeme
Re: White Metal Soldering
Posted: Sat May 04, 2019 3:09 pm
by philipy
Re: White Metal Soldering
Posted: Sat May 04, 2019 3:10 pm
by tom_tom_go
There are loads similar to what Graeme mentioned on eBay for under £3 with postage.
Thanks for the suggestion!
Re: White Metal Soldering
Posted: Sat May 04, 2019 3:13 pm
by philipy
Tom, some of those say "steel" rather than the brass which Graeme recommended, and some say 'sponge' without defining.
Re: White Metal Soldering
Posted: Sat May 04, 2019 3:26 pm
by tom_tom_go