Page 1 of 16
Wild Rose ~ Quarry Hunslet
Posted: Fri Dec 18, 2015 8:02 am
by dewintondave
I am enthused to build Dave Watkins' Wild Rose III as my next loco build project.
The drawings have been kindly made available for download, and are now the Association of 16mm Narrow Gauge Modellers website:
https://www.16mm.org.uk/
Posted: Fri Dec 18, 2015 12:50 pm
by Joe
Its a good project, best of luck, will you make all the components yourself?
Posted: Fri Dec 18, 2015 2:13 pm
by Peter Butler
That is a lovely little loco and judging by your previous builds you will make a first class job of it. I do hope you go ahead and keep us all posted as you go.
Posted: Fri Dec 18, 2015 2:17 pm
by Annie
That's a really nice loco, I wouldn't mind having a go at that myself

Posted: Fri Dec 18, 2015 2:19 pm
by Busted Bricks
I seem to recall that some parts are available laser cut from Model Engineers Laser.
EDIT: They are!
http://www.modelengineerslaser.co.uk/lo ... ocotype=16
Posted: Fri Dec 18, 2015 11:48 pm
by dewintondave
I have always made all the parts myself before, but possibly I may buy some fittings.
I'm scaling the plans up to suit the big De Winton in my profile pic. The De Winton has a 4' wheelbase, where as Wild Rose has a 3' 3" wheelbase.
Posted: Tue Dec 22, 2015 8:06 am
by dewintondave
A start has been made; wheel blanks. I faced off, rough turned the OD, and sawed the blanks off at work today. These wheels are going to have LGB style 3 mm deep flanges.
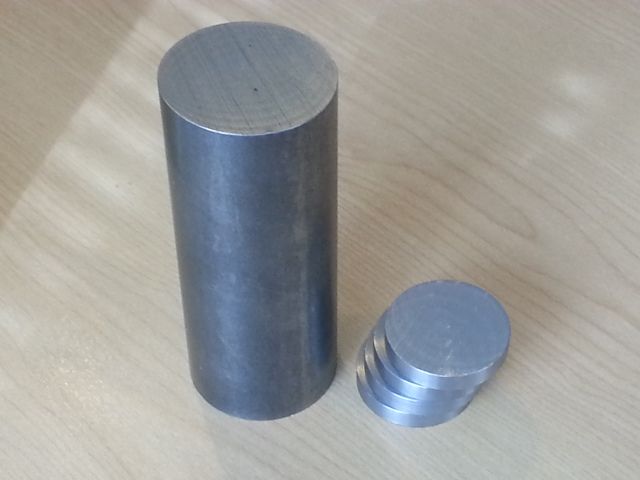
Posted: Tue Dec 22, 2015 8:22 am
by Keith S
Well this will be interesting.
Posted: Tue Dec 22, 2015 8:48 am
by -steves-
dewintondave:115036 wrote:A start has been made; wheel blanks. I faced off, rough turned the OD, and sawed the blanks off at work today. These wheels are going to have LGB style 3 mm deep flanges.
Best wishes,
Dave
Marginally off topic, but......
Can I ask a dumb question and one I have wondered for a while. Now you have cut the wheels from the bar, how will you make the flanges and any dish or recesses in the wheels as I would not know where to start to mount this in a lathe now? Drill the middle and put a bolt through it? I just don't know? I would be very interested to see this done as I have some bar for wheels but honestly don't know where to start

Posted: Tue Dec 22, 2015 9:29 am
by Annie
Sigh, I used to make my own wheels on my lathe too, but with this disability I now have any kind of power tool use is a complete no no

Posted: Wed Dec 23, 2015 7:42 am
by dewintondave
-steves-:115040 wrote:Can I ask a dumb question and one I have wondered for a while. Now you have cut the wheels from the bar, how will you make the flanges and any dish or recesses in the wheels as I would not know where to start to mount this in a lathe now? Drill the middle and put a bolt through it? I just don't know? I would be very interested to see this done as I have some bar for wheels but honestly don't know where to start

I'll chuck them one at a time in my 3 jaw chuck and drill and ream the bore. All the turning will be with the blank mounted in a mandrel held in the chuck.
Here's a picture from 2006 of the between-centres mandrel on my Unimat 3 lathe turning a wheel for the large De Winton. It's 40 mm tread diameter with a 2.5 mm flange depth.
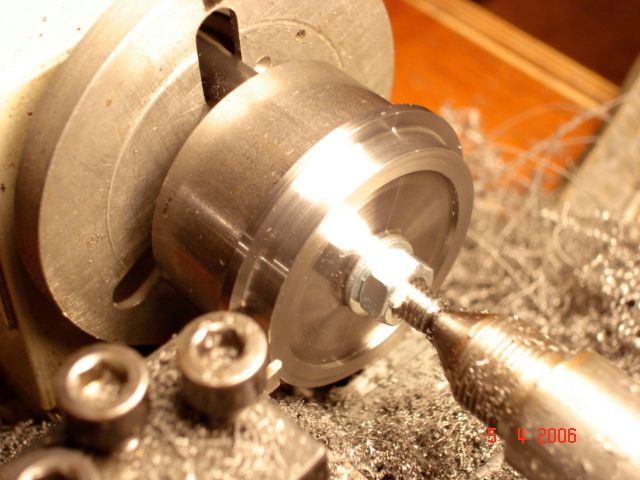
Posted: Wed Dec 23, 2015 8:32 am
by -steves-
That is brilliant, thank you. It gives me an idea of how I can do my own wheels now. What angle is the wheel flat that runs on the track done at? I think I may struggle trying to part off these in my lathe, so I may well cut up cutting them in a band saw, then putting them in the mill to get them the same thickness and smooth them off.
Looking forward to seeing this project progress.
Posted: Wed Dec 23, 2015 10:34 am
by GTB
-steves-:115059 wrote:That is brilliant, thank you. It gives me an idea of how I can do my own wheels now. What angle is the wheel flat that runs on the track done at? I think I may struggle trying to part off these in my lathe, so I may well cut up cutting them in a band saw, then putting them in the mill to get them the same thickness and smooth them off.
Like Dave I cut my wheel discs with a bandsaw, as my chinese 7x12 mini lathe hasn't got a hope of parting off mild steel that dia.
I grip the discs in the 3 jaw chuck with a spacer behind them then face them off on both sides. A carriage stop for the lathe is useful for making sure they all come out the same thickness. My bandsaw cuts square so the surface of the blanks just needs a skim.
Keith Bucklitch has some good instructions on turning wheels as part of his Brazil instructions.
http://trains.de.jardin.free.fr/minidam ... heels.html
The carriage stop also comes in useful when turning the wheel profile. My mandrel is marked (as is the chuck) and always goes back in the lathe in the same position. My wheels typically come out with eccentricity no more than 0.02mm. If it's more than that, the mandrel needs some attention.
Since my models are all 45mm gauge, I use the G1MRA wheel standards, with a 3deg tread taper, but with a modified flange profile. It isn't strictly necessary to taper the tread with models, but it looks better. Not all real railways use tapered treads if it comes to that.
The curved fillet between the tread and the flange is more important than tapered treads for good running, as is a slight taper on the back of the flange. I use a profile similar to this one.
https://16mm.org.uk/newsite/files/default.html#wheels
Regards,
Graeme
Posted: Thu Dec 24, 2015 6:37 am
by dewintondave
All this talk of wheels + the poor weather = lathe work. It's been a long time since I last turned some wheels.
This is how I chucked the blank
Here it is, faced, drilled & reamed bore, recess cut
I need to do this to all four wheels, then it's time to get the mandrel out.
The treads will be turned with a 3 deg. taper. I've sort of developed my own wheel spec for these deep flange wheels. 7 mm wide with 39.5 mm back to back for my 45 mm track. The steam diesel and live diesel both have these wheels.
Posted: Thu Dec 24, 2015 9:40 am
by GTB
dewintondave:115085 wrote:All this talk of wheels + the poor weather = lathe work.
There's a blocking high over the Tasman, so too hot to be in the workshop here and tomorrow is even hotter with a severe fire warning. Sigh....
What tool have you used to recess the front of the wheel? I ground up a special for that job, but sometimes run into problems with chatter.
Regards,
Graeme
Posted: Fri Dec 25, 2015 5:33 am
by dewintondave
Merry Christmas all
GTB:115090 wrote:What tool have you used to recess the front of the wheel? I ground up a special for that job, but sometimes run into problems with chatter.
I'm using the round nose finishing tool that came with my Unimat 3 lathe all those years ago. I'm taking .010" depth cuts with it.
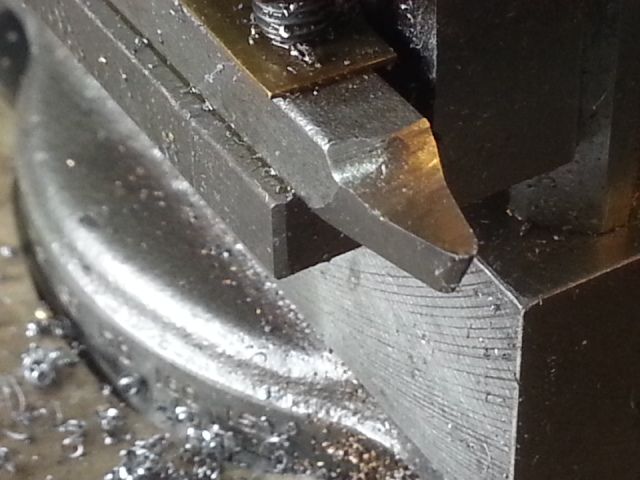
Posted: Sat Jan 02, 2016 4:15 am
by dewintondave
Happy New Year
With the latest spell of bad weather I have finished the wheels.
Paint drying in the sun - a few days ago
Front face skimmed. Tread rough turned on the mandrel
Finish turning the 3 deg. coned tread and flange with a form tool. The flange is formed
Finished wheels
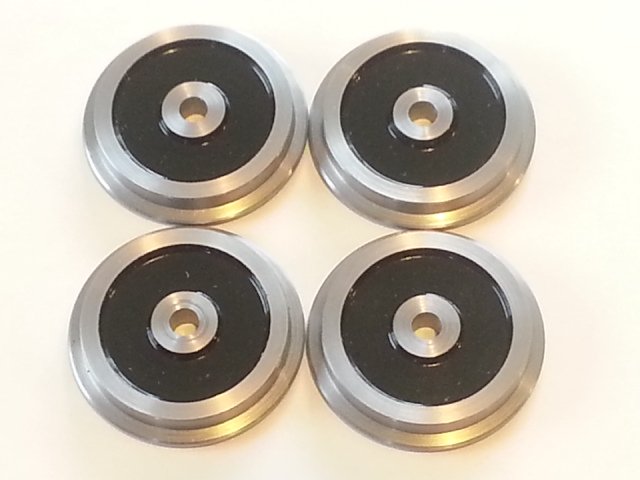
Posted: Sat Jan 02, 2016 7:55 am
by Annie
Very nice indeed Dave

Posted: Sun Jan 03, 2016 11:45 am
by -steves-
Awesome, totally awesome, and probably inspiring enough that I may well give mine a go this year sometime

Thank you

Posted: Sat Jan 09, 2016 11:38 pm
by dewintondave
Project scope creep! I'm now favouring the Hunslet Large Quarry Class. It's very similar, the wheelbase is increased from 3' 3" to 4'. Fortunately the wheels are the same diameter. Here's a fine example:- Hugh Napier
